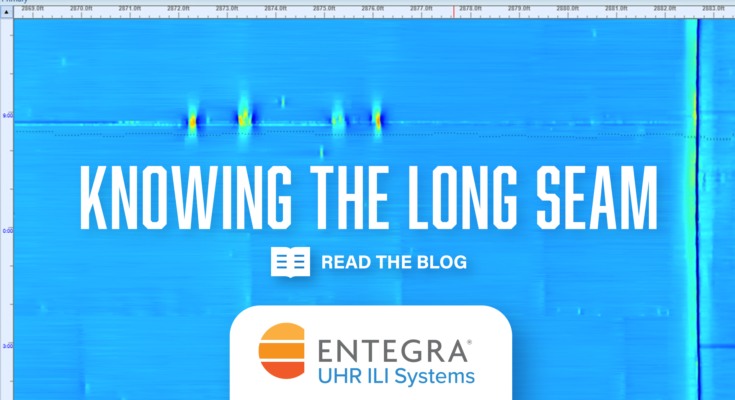
Knowing the Seam Weld: Essential Insights Using UHR Axial MFL
The technologies behind axial magnetic flux leakage (MFL) in-line inspection (ILI) have come a long way. And they continue to evolve. This is especially true with regard to integrity threats to the seam weld. Many misperceptions still exist about the ability of MFL to deliver with regard to POD, POI and sizing of seam-weld anomalies. …
The technologies behind axial magnetic flux leakage (MFL) in-line inspection (ILI) have come a long way. And they continue to evolve. This is especially true with regard to integrity threats to the seam weld.
Many misperceptions still exist about the ability of MFL to deliver with regard to POD, POI and sizing of seam-weld anomalies. For previous generation MFL ILI, just seeing the seam posed a challenge. In truth, the capabilities of MFL – and the ability to extract nuanced data from it – have grown exponentially beyond what was previously thought possible.
Driving this evolution? The advent of Ultra-High-Resolution (UHR) technologies backed by tech enabled, human-based insight, vision and analysis. We are now able to capture more data than ever and, most importantly, extract more knowledge from it. The ability of operators to see more and know more about their pipelines allows them to address seam weld anomalies accordingly and keep their assets running safely and efficiently.
Technology
There is no real industry standard for what constitutes Ultra-High-Resolution, which has led to the term being overused and, in some applications, mis-used.
ENTEGRA true Ultra-High-Resolution (UHR) technologies employ state-of-the-art electronics and a higher concentration of primary axial sensors, a larger number of secondary sensors like ID/OD and a dense array of caliper sensors for mapping the surface of the ID wall. This gives the UHR platform an incredible POD and POI on all aspects of anomalies detectable by MFL technologies – and some previously considered virtually impossible to detect.
Data Analysis
A true UHR AMFL system also incorporates truly unique Data Analysis (DA), which can provide nuanced assessments and recommendations to the operator. That is why automation alone and black-box DA assessment cannot replace human experience-based insight and deduction.
It’s this combination of technology and experienced insight that allows ENTEGRA to detect, characterize, and assess not only the seam, but anomalies coincidental to or preferential to the seam. And this is all the more critical, given that there is a myriad of other variables that need to be considered. Different seam types, the age of the pipe, varied manufacturing methods and the construction and welding processes behind the pipeline itself all impact an accurate assessment of the long seam.
No wonder there are so many misperceptions of MFL performance with regard to assessment of the seam weld. All of which can now be dispelled with the ENTEGRA system helping pipeline operators to see more, know more and efficiently, effectively and safely prioritize their dig programs.