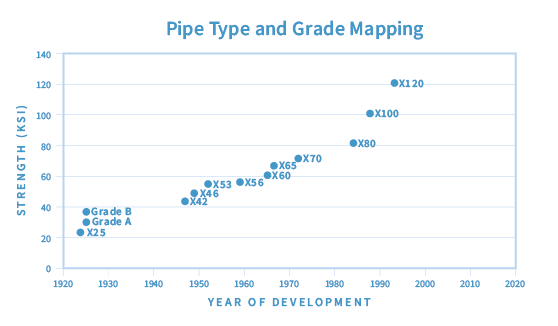
ENTEGRA Pipeline Inspection: A Case Study
How we helped a South Texas company to obtain a high MOAP with a True UHR inline inspection. Challenge A South Texas pipeline operator hired ENTEGRA to perform a materials classification report to fill in the gaps on a run of pipe with a vintage that spanned over 60 years (1952 to 2016) while confirming …
How we helped a South Texas company to obtain a high MOAP with a True UHR inline inspection.
Challenge
A South Texas pipeline operator hired ENTEGRA to perform a materials classification report to fill in the gaps on a run of pipe with a vintage that spanned over 60 years (1952 to 2016) while confirming historical data. Their goal was to obtain the highest possible MAOP by truly knowing their pipeline.
This pipeline contained eight different wall thickness, six known pipe grade differences, and five pipe types (Spiral, DSAW, ERW, Flash Welded and SSAW). In addition, this 59-mile run included pipe from nine different manufacturers with various pipe material combinations. With all this variety found in the pipeline, the operator found that complete records had been lost in some of the historical pipeline documentation. These lost reports included numerous digs that each required single joint replacements. These records contained scattered and disjointed data on wall thickness and pipe type, and nothing concerning pipe grade.
Technical Details
Data needs context to unlock its value. Validating these single joints for a material classification report includes knowing each joint of pipe’s diameter, wall thickness, pipe type, and pipe grade. Even though the operator’s data was incomplete, it doesn’t mean it wasn’t useful. For example, the correlation of historical data with our UHR data gave ENTEGRA’s Data Analyst team a starting point to begin compiling the material classification report.
Considering the identified variables, a systematic approach was developed to create a baseline of verified data. By sorting features into like bins, we could begin to identify if any abnormalities existed within the results. Through this approach we were able to identify sections of outlier X70 pipe. The X70 grade was determined as there was other recorded documentation of X70 pipe in the pipeline and the ILI tool readings suggested there was a correlation to these values.

Outcome
Utilizing multiple datasets that the 30” UHR MFL combo tool’s various sensors gathered in a single run, our Data Analyst team was able to classify pipe grades for seamless and seam type pipes, all without any calibration digs. In addition to the materials classification report, we also detected, identified, characterized, and sized a range of pipeline threats including pinholes, pits-in-pits, long-seam corrosion, manufacturing flaws, physical damage, and previous repair structures.
The ILI tool’s data correlated well with the pipe records, but in addition, it located joints that were not accurately documented. This alleviated any doubts or concerns the operator had, who consequentially was not required to classify any unknown pipe joints to the regulatory standard SMYS value of 24,000 psi.
Download our Pipe Grade Paper
Intrigued? Download our Pipe Grade Paper by filling out the form below.